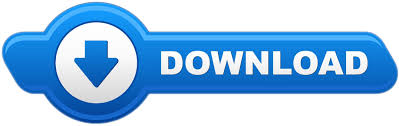

Flow visualization is provided through color maps of local Mach number, density, pressure, and temperature, including streamline plots.
Amateur car body design competition 2017 software#
Some modeling software provides both solid and surface modeling capabilities.ĢD CAD software provides 2D drafting capabilities.ĢD and 3D Virtual Wind Tunnels software packages for Microsoft Windows.įrom the maker: "MicroCFD analyzes 2D and axisymmetric subsonic, transonic, and supersonic flow (Mach 0.1 to 10) over multi-element configurations on a Cartesian cut-cell mesh.

If they are “parametric”, part dimensions and properties can be adjusted using parameters or even other parts, enabling things like auto-sizing.ģD surface modelers enable the creation of what are called NURBS curves, which form complex flowing shapes that are useful in creating stylized bodywork. Software for creating models of your car concept or detailed design.ģD Solid modelers provide the ability to create parts, connect them to make assemblies, and ultimately a complete vehicle if desired. Planning – Determining the course of the project through the development of high level tasks through to detailed level tasks.Ĭonceptualizing – Preliminary ideas relating to a whole car design or to components.ĭocumenting – Documenting ideas, decisions, plans and todo lists. Task management – Managing the people and tasks to ensure they are completed in the order they should be and in the time duration expected. Task identification and Critical path identification – Identifying tasks that must be performed to build the car and where bottlenecks may occur that could delay the project. Vehicle dynamics simulation – Using a 3D solid model with defined suspension pivot point and mass distribution, simulate the expected motion of the car in various tests, such as over bumps, around corners. Suspension Geometry – Used to determine the basic suspension geometry before applying the suspension pickup points to a 3D solid model or 2D CAD chassis/frame Torsional Rigidity – Using a 3D solid model, simulate torsional rigidity testing by constraining one end of the chassis and applying a load torsionally and determining the degree of twist. Structural Fatigue simulation – Using a 3D solid model, simulate cyclical loads and determine cycles to failure such as might occur during operation on bumpy roads. Structural strength – Using a 3D solid model, constrain (Hold steady) one part of the chassis, and apply loads to another part to determine the strength and ultimate buckling characteristics. Powertrain Modeling – Model powertrain components like engines, transmissions, transaxles, differentials, driveshafts, propeller shafts for integration into an overall vehicle model.īody shape – Most flexible means of modeling complex body shapes or bodywork, including sheet metal, for potential later use in aerodynamics simulations (CFD) and build reference measurements.ĭrawing creation – For basic dimensional drawings of all aspects of a car design to be used as build plans and reference measurementsĮfficiency – Using a 3D Solid or surface model, simulate air flows and assess the drag co-efficient of the vehicle and make improvements before re-simulating.ĭownforce – Using a 3D solid or surface model, simulate air flows and determine lift/ downforce at various points of the bodyĭiscrete Aero Component testing – Using a 3D solid or surface model or 2D section drawing, simulate air flows and determine the lift/drag characteristics of the componentĬhassis /Structural Design /FEA (Finite Element Analysis) Suspension Modeling – Model suspension components like wishbones, shocks, springs, steering, brake rotors, axles, wheels and tires for integration into an overal vehicle model
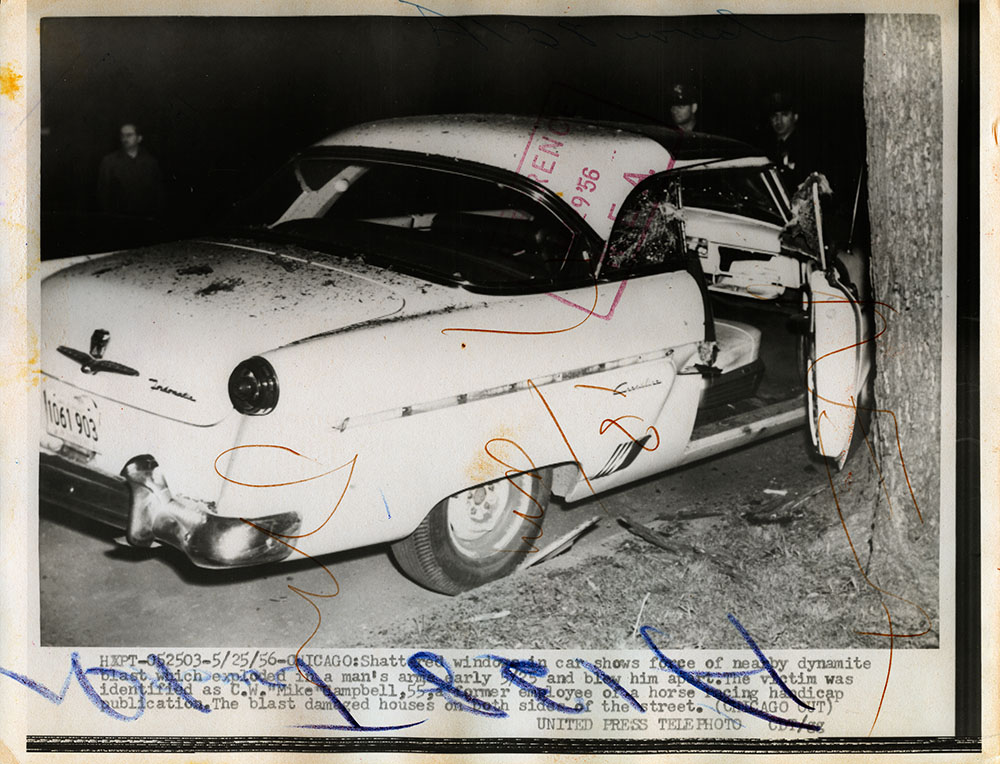
Part Modeling – Model general parts like seats, pedals, brake master cylinders for fitment and assembly into a chassis model. Use the table below to learn how different types of software are used to engineer a vehicle design: Software Typeīody shape – Model car body shape or bodywork, including sheet metal, for potential later use in aerodynamics simulations (CFD) and build reference measurements.Ĭhassis/Frame Modeling – Model space frame tube chassis structure and mounting brackets for potential later testing in structural design simulations (FEA) and build reference measurements. Guide To Car Design Software and Its UsesĬar design software can be used to model or simulate almost every aspect of an automobiles structure or operation.
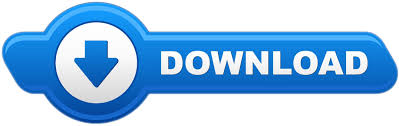